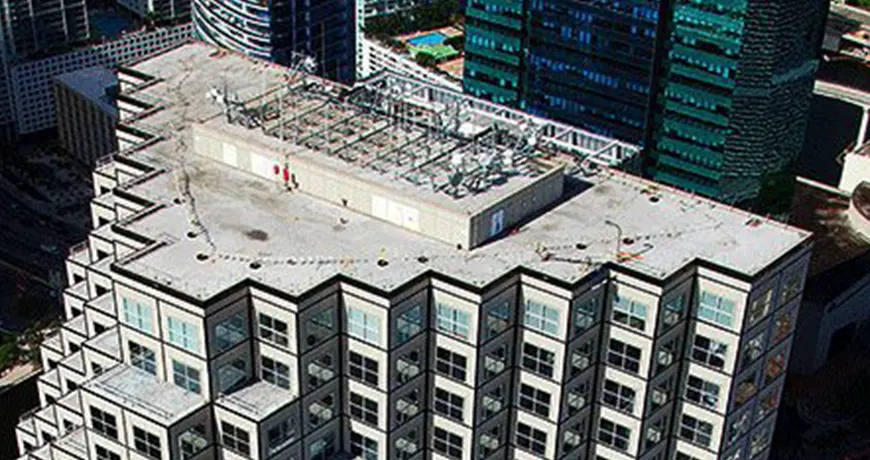
Southeast Financial Center
Southeast Financial Center is the tallest office tower in Florida and the second tallest building in Miami. Topping more than 765 feet, the 55-floor building was constructed in 1984 and is home to more than 79 businesses including the United States Postal Service, Goldman Sachs, and the Canadian Consulate.
In 2013, Advanced Roofing Inc. (ARI) was selected by Facility Engineering Associates, Southeast Financial Center’s roofing consultant, to re-roof the office building in downtown Miami due to pre-existing leaks under the roof system’s concrete overburden which made it difficult to locate and more costly to repair. Facility Engineering Associates secured ARI for this project because of its proven track record of completing difficult commercial re-roofing projects on time and within budget. With in-house divisions including metal fabrication, crane, air conditioning, roofing, and lighting protection, along with a healthy balance sheet and commitment to safety, ARI offers unmatched commercial roofing solutions that distinguish it from traditional roofing contractors. Many of the company’s in-house divisions were used for this project.
Working on a fully-occupied business building in a bustling downtown area brought with it a unique set of challenges along the way, but also quick-thinking problem-solving:
Challenge #1 (and the biggest): Removing tear-off debris and loading materials onto the 56th floor (roof) of a high-rise in the heart of the Financial District
ARI tore off the existing concrete overburden, insulation, and waterproofing system. There was up to 4.5” of concrete and 2” of insulation, totaling 860 cubic yards of concrete removed in addition to the insulation. The concrete was recycled. With no access around the building for a tower crane, the concrete had to be cut into 12” x 12” squares to unload off of the roof. The lower roof had a large antenna farm in place with 143 penetrations that had to be cut around. The existing concrete also had rebar loops that had to be hand cut and then the concrete deck was repaired, certified, and tested for moisture prior to the Kemper primer install. The Kemper Roof System was selected for its ability to meet very high pressures on a 55-floor building in a High-Velocity Hurricane Zone.
All materials had to be removed from the roof via a hoist through an air shaft, maneuvered through a mechanical room (all with ramps built over the drains and conduit on the floor of the mechanical room), then taken in a passenger-style service elevator down 54 flights. Once off of the elevator, materials were moved through a service corridor, to another elevator, up another floor, and out to a bay loading dock that we only had access to from 7 pm to 5 am, and had to share with other contractors during the week. Additionally, we could only use the elevator after 2 pm on Saturdays; only on Sundays did we have full control of material transportation to the roof. The round trip for each load was approximately 45 minutes, and there were many trips that had to be taken due to the elevator’s 5,000 lbs. maximum capacity, with load centering requirements, greatly reducing the amount of debris that could be moved at one time. Using 8, 1/3 yard dump hoppers, 6 pump pallet jacks, and two electric pallet jacks, our team was able to coordinate moving material efficiently with the service elevator without bottlenecks.
A new Kemper waterproofing system and new insulation were installed, and new concrete was poured. The concrete had to be mixed on the roof with 10 small mixers. There were 11,205 50-pound bags of concrete mixed in total. All had to be taken up to the roof via the same route the debris came down. Using an eight-man materials train, our crew was able to keep a steady supply of materials to the roof without delaying the production. Due to the elevator centering and capacity, it took 225 trips from the loading dock, up both elevators, through the access route, and up to the roof for loading the concrete alone. ARI performed adhesion tests on the Kemper system each step of the way and performed flood testing prior to starting the concrete pour. Once pouring began, ARI also sent cylinder tests out for compression strength testing since all concrete was being hand-mixed from bags while on the roof.
Another challenge to completing the Kemper roof system was that it needed to be installed under direct sunlight. As our team was not permitted to work during daylight hours Monday – Friday, it was critical l for our in-house teams to work together smoothly on weekends so that we could finish the project on time.
With only one service elevator going to the 54th floor, the ARI team had to use the emergency stairwell to access the roof on the 56th floor. The elevator was also shared by all other contractors and staff doing work in the building. At times there were 12 floors that were under renovation, with numerous contractors per floor including Fed-Ex and UPS pick-ups at the start of our weeknight shift. It wasn’t unusual to wait more than 15 minutes for the elevator each trip.
Challenge #2: Updating the building’s systems
Southeast Financial Center rents the roof space to other companies to house their antennas. ARI installed all new antenna supports on the upper roof which required all tenants to relocate their antennas from the lower roof to the upper roof. Supports were also installed for all of the cables. Trays were purchased from US Cable Tray and custom ladders were made to install on the horizontal runs. ARI worked around the antenna contractors, monitoring their schedules to have them complete their moves on time so the ARI team could proceed with their work.
A new safety railing was also installed to meet OSHA requirements. Upon completion, the building procured new window washer rigs but the new railings did not accommodate the new railing. ARI worked with the manufacturer and consultant to revise the railings to accommodate the new rigs. New anchors were also required which required subcontract installation and testing for safety compliance. ARI’s in-house Lightning Protection Division removed, reinstalled, and re-certified the building’s lightning protection system, incorporating the new antenna farm into the protection. The in-house sheet metal shop fabricated new 24-gauge stainless steel counter flashing and pitch pans to go around all of the anchors.
Challenge #3: Scheduling
Due to noise ordinances and odor, work could only be performed at night. However, ARI was not able to install the Kemper system during night hours, so this project was performed with a large crew on Saturdays and Sundays. Concrete cutting, removing, and loading occurred during night hours Monday through Friday. ARI installed metal halide balloon stadium lights to allow workers to see at night.
Challenge #4: (Unexpected) Buzzards
The birds would continuously eat the Kemper primer and sand during installation. The team had to make more than 100 repairs then finally installed safety flags and had people monitor all around the roof to keep the buzzards away so the work could be completed.
Despite the challenges, the Southeast Financial Center project was completed on time and to the client’s satisfaction.