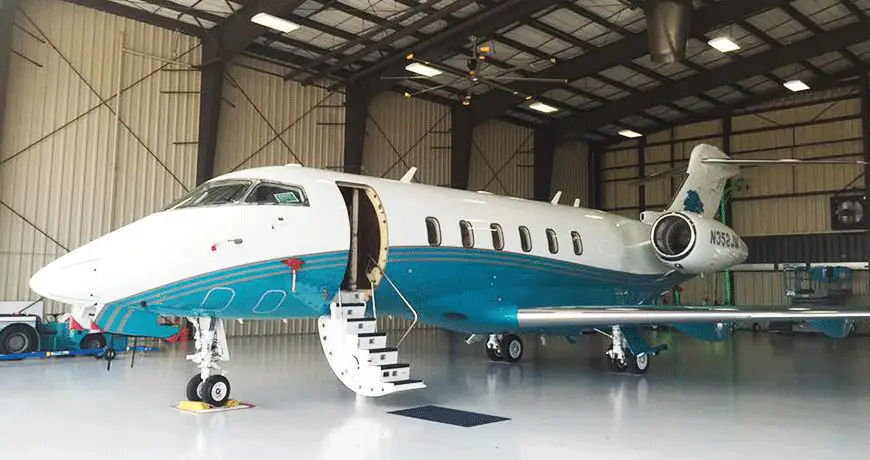
JM Family Aviation Hangar
JM Family Enterprises, Inc., the world’s largest independent distributor of Toyotas, has a corporate flight department and a company-owned fleet of four jets at Fort Lauderdale Executive Airport in South Florida. When the roof on their 36,400-square-foot aviation hangar began experiencing leaks, Advanced Roofing, Inc. (ARI) was selected to retrofit the existing roof with a new roof on the 50-foot tall hangar.
An aging standing-seam metal roof with sealants breaking down between seams and laps of the metal panels was producing leaks inside of the facility. Additionally, jet fuel and debris from the hostile airport environment were causing the roofs to prematurely deteriorate. This was a particularly urgent issue to fix as the jets inside of hangar are valued at more than $50 million. The client previously performed coatings to prolong the roof’s life, but a custom, long-term solution was essential. Having worked with JM Family Enterprises in the past, ARI upheld the client’s high standards regarding the quality of work and upkeep of the hangar while repairs were being made.
Scope of Work
To repair the system, ARI retrofitted a metal roof to a single-ply membrane using an 80-mil PVC membrane from Sika Sarnafil. PVC is the preferred solution for systems in harsh environments, and 80-mil membranes are ideal for Florida roofs as they are extremely durable and the strongest on the market. A Rhinobond heat induction welding system was used to attach the membrane, meeting hurricane wind codes. In addition, laps between the metal roof panels were filled using a custom cut 2.8- inch thick, 17-inch wide Flute-Fill polyiso; and a 25-inch Densdeck cover board was installed to produce a completely smooth surface. A custom drainage solution was also created for infilling the existing built-in gutters and creating retro drains at the existing downspout drops. As an added benefit, the system is more energy efficient than the existing metal roof, making it an ideal fit for the JM Family aviation hangar.
To ensure the customer’s future safety when accessing the new roof, Tri-tech fall protection tie-offs and a rail system were used around access points, and ARI installed new walk pad walkways for safe access routes.