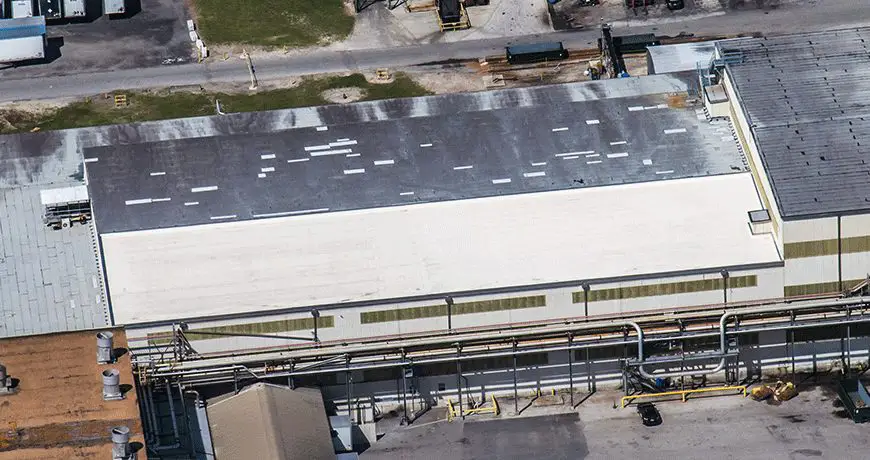
WestRock Paper Mill
WestRock is a leading global packing company focused on customers, innovation, and operational excellence. The company aspires to be the unrivaled provider of paper and packaging solutions in global consumer markets. WestRock has 275 operating and business locations in 30 countries spanning North America, South America, Europe, and Asia-Pacific.
The company’s Paper Mill Building 5 located in Jacksonville, Florida features a 40-foot high, 18,000 square-foot roof which was in need of replacement due to persistent leaks and a highly sensitive manufacturing environment. The original roofing consisted of precast concrete slab deck panels, three inches of foam glass insulation, and a built-up pitch roof with gravel. Advanced Roofing Inc. (ARI) was selected to replace the old roof system with a new one that would ensure long-term manufacturing productivity for the client.
The 14-person crew began work on the building on November 1, 2015, utilizing FiberTite single-ply PVC. The crew began by removing all roofing and sheet metal. Insulation boards and membranes were glued on half of the roof. However, the other side of the roof required the removal of all precast concrete slab decking; scraping, priming, and painting all of the metal supports; and installation of new 18-gauge stainless steel decking. A Soprema vapor barrier was installed across the roof and the crew mechanically attached insulation boards and membrane. The ARI team also reconfigured the drainage on the building since the original system was designed in a way that had the roof sloping to gutters and downspouts. The client wanted to change the roof to a parapet wall with scuppers.
ARI’s goal was to give the client a cleaner, more professional roof. After consulting with the client, a temporary roof was installed so as to not flaw the new white membrane. As part of this process, the crew removed the gravel, tore off the built-up roof then installed a temporary roof. Much of this work had to be done while fully tied off as the plant’s safety requirements far exceeded OSHA standards. During the process, all materials had to be brought to the roof by use of a crane, and trash could only be removed by use of a crane as well.
Working on a highly productive building containing sensitive machinery and an active workforce brought with it a unique set of challenges along the way including:
Challenge #1: Safety
Creating and maintaining a safe work environment for the building’s employees and machinery was a top priority for the client, therefore it became a central focus of the project. The paper mill provided two full-time safety coordinators for this project. However, each coordinator provided a different set of rules while on site, causing a delay in productivity when the rules that were approved one day were not effective the next day.
In addition to the roofing system, ARI was required to install a temporary sub-deck on the inside of the building to protect the manufacturing equipment and the workers while the decking and roofing were removed. The crew installed 20-foot aluminum beams spanning from truss to truss, then laid ¾-inch plywood across the beams and lined them with plastic. This process posed a unique challenge since there were no trusses to rest the beams. To circumvent this issue, the crew suspended heavy-duty cable rigging from higher supports and then suspended the beams the same way in order to protect the machinery.
A full perimeter warning system of cones and flag lines was also installed. In addition, two Raptor fall protection carts were used during periods when crewmembers were closer than six feet from the edge. The same procedures were used while the crew was removing and re-decking the side which needed the concrete slab removal. A full-time safety monitor was used in addition to the safety cart while working at the edges.
The client required regular inspections by the membrane and the adhesive manufacturer. A pull test is required at the end of the project.
Challenge #2: Production Delays
This project experienced unexpected delays caused by weather, as well as a few caused by difficulties with the current roofing system. The ARI team worked closely and efficiently to get through the delays and rectify issues to minimalize impact. Removing the decking was a considerable challenge initially. This process was extremely slow, causing a lack of production each day during this stage in the project. During the first week, ARI was only achieving five square feet of tear-off a day. By altering the removal process through the use of alternative tear-off tools, the project was back on track with a speedy removal of the system. Within a couple of weeks, the crew was up to 10 to 12 square feet a day.
The decking installation and mechanical fastening also took longer than expected. The 18-gauge stainless steel decking proved to be too hard to drill through with the standard manufacturer-provided screws, causing the need for predrilling the entire roof assembly. In addition to these challenges, an unexpected rainier-than-usual winter caused the job to be shut down for a day, sometimes two, almost every week.
The challenges mentioned above have caused a very minimal delay in the overall project, with completion anticipated in the next few weeks. However, despite this slight setback, the client is more than satisfied with the project. ARI was informed at the beginning of this project that the client has high expectations and is very involved and vocal with all projects. Their safety regulations and rules are also more demanding than what most contractors are used to, so trust is of utmost importance to this client.
Through good planning, communication, and execution, this potentially difficult project has run smoothly and ARI anticipates being contracted by WestRock for future projects.