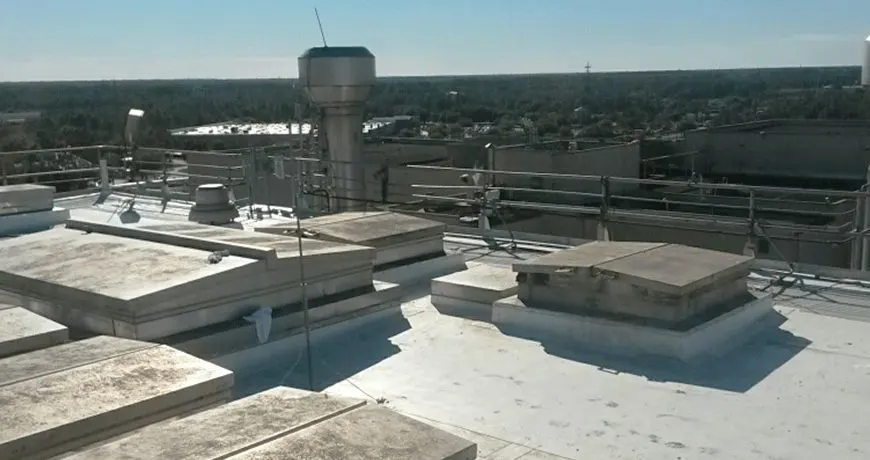
Anheuser Busch Grain Silo
Advanced Roofing, Inc. (ARI) was hired by the iconic Anheuser-Busch Company based in Jacksonville, Florida to complete a difficult restoration of a 6,000 sq. ft roof on their Grain Silo. The pre-existing roof system, which had many leaks, was located 110’ off the ground and had smoke hatches covering 25% of the roof. At the end of its service life, temporary fixes were made over time; however, these constant repairs were increasing the operational budget while the issues remained unresolved. The roofing system was at risk of eventual failure and was prohibiting the company from making essential renovations inside the building.
This month-long project included the removal of the existing built-up roof, insulation, and metal flashings down to the existing concrete deck. Followed by the installation of the new roof system, which consisted of foam down tapered ISO, DensDeck cover board, and a fully adhered Sika Sarnafil 60 mil G-410 single-ply membrane. While a seemingly small project in size, the Anheuser-Busch Grain Silo re-roof presented many challenges that the ARI team was able to handle quickly and professionally, providing the client with a long-lasting roof system, under budget, and with a 20-year No Dollar Limit Warranty.
Challenge #1: Risk of Explosion
The Grain Silo is used for grain storage, which presented a risk of explosion if the grain or grain by-product is exposed to flames or sparks; making the tear off of the existing roof a dangerous challenge as the client prohibited ARI from using gas-powered or grinding tools that create a spark. The solution was to remove the roof with hand tools, which was time-consuming and difficult. Also, there were 20 smoke hatches that consumed 25 percent of the roof. The hatches were less than a foot apart and completely covered in stainless steel flashings, requiring tools specially engineered to tear off and install the new roof system around them.
Challenge #2: Access and Location
The Grain Silo is nine stories (110’ tall) and was 30’ from the nearest staging area, which meant that only a few hundred pounds of debris could be removed at one time. This resulted in a tremendous amount of lifts to get trash down, and materials had to be brought up in small quantities.
Once safely on the roof, the team realized that a nearby production building released a cloud of vapor every half hour that would wet the roof, making it difficult to weld the roof membrane when wet.
Challenge #3: Safety Railing Obstacle
A final challenge the ARI team faced was a safety railing mounted to the concrete deck that encompassed the entire perimeter of the building. Not only did this cause dozens of extra penetrations that needed to be flashed, but it also made installing the insulation and edge metal increasingly difficult as workers had to squeeze between the narrow railing to work at the roof’s edge. With careful precision and appropriate safety equipment, the ARI team was able to secure the boards and membrane safely without disrupting the facility’s operations.
Our Solutions
With an experienced team, ARI was able to quickly and adequately solve issues that arose during the project. Our team’s approach was simple – we anticipated potential problems and had multiple solutions available. This job also required careful preparation and coordination with the facilities operations team to deal with the high level of potential safety hazards along with multiple scheduling conflicts with brewery operations during the holiday season.
In addition to providing the client with a safety plan before starting the project, ARI also placed it most experienced foreman with more than 30 years in commercial roofing on site for the project. He had every safety training certification available and was able to maximize our team’s safety and productivity. In addition, to fall protection training, the team utilized retractable lanyards, fall protection harnesses, hard hats, ear, and eye protection.
With the diligence and expertise brought to all ARI projects, the team was proud to provide a trusted Sika Sarnafil roofing solution that also allowed Anheuser-Busch to complete renovations inside of their building, which was previously on hold due to the leaks. Our team’s attention to detail, expert problem-solving, and focus on safety resulted in saving money for the client while providing a proven roofing solution, making Advanced Roofing, Inc. the ideal candidate for a Sika Sarnafil Project of the Year award.