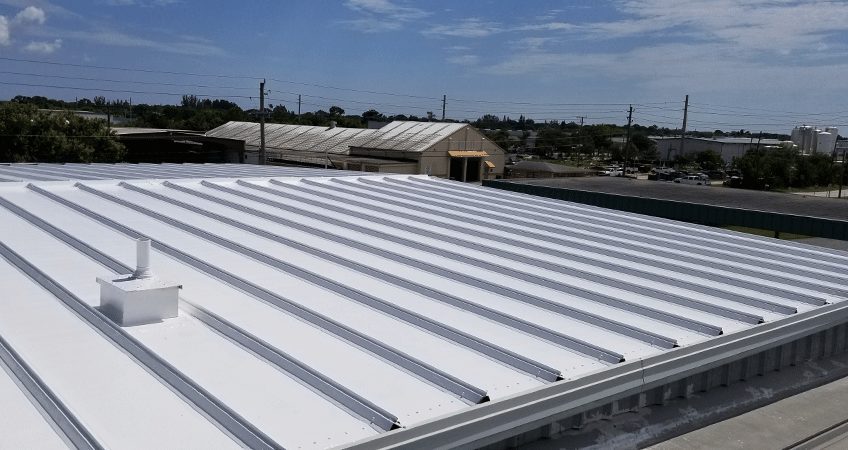
Extend Your Roof Service Life With A Commercial Roof Coating
Flat roof coatings can be a cost-effective way to extend the service life of your commercial roof while lowering energy expenses.
A lot of strain can happen to a commercial roof in Florida. From taking on hurricane-force winds to the constant beatings of summer’s rainy season and excessive heat, the surface of your roof is constantly taking a beating. Replacing your roof is not only a major expense but can also impact your business. Roof coating systems solve these problems by providing a reliable roofing system with a low installation cost.
A flat roof coating can be the right choice for commercial property, especially in a time when labor costs and environmental concerns are rising. A coating acts as a barrier to help protect the roof from the elements by increasing UV protection to fight against the sun’s harmful rays and helping to reduce the building’s energy costs.
Roof coatings are liquid-applied and provide a monolithic, uniform membrane that helps protect and preserve the underlying roof system. They can be applied by spraying or roller application with additional fiber reinforcement around the flashings, roof penetrations, hatches, and other rooftop equipment. The end result is a completely sealed and waterproofed system. They can be applied to (most types of roofs) and are an alternative system that works along with your current roof.
What are the benefits of a roof coating system?
- Increase Roof Life: A coating can help extend your roof service life up to ten years.
- Reduce Energy Use: The reflective and emissive properties of many coatings result in decreased roof temperatures and energy use requirements during daytime hours, reducing the load on the HVAC system.
- Aesthetic Improvements: Rather than replacing an unsightly, aging roof for aesthetic purposes, managers can improve the appearance of a roof that is visible from the ground or adjacent buildings through the application of a coating.
- Microclimate management: in many low-slope roofs, areas of ponding water can occur. In these localized areas, many types of roofing membranes are prone to premature deterioration and eventual leakage. Using carefully selected coating products and applications in these affected areas can prolong the life of the entire roof system
- Cost-Effective: Since they are applied directly on top of your existing roofing system, roof coating systems are easier and quicker to apply, so they don’t require the amount of labor that comes with a new roof installation, thus saving time and money. Commercial roof coating lasts up to 10 years when maintained properly.
- Heat Reflection: A highly-reflective roof coating reduces energy costs and provides UV protection for your roof. It reduces heat transfer into the building, decreasing thermal shock (thermal expansion and contraction of the roof membrane) and adding years to your roof while reducing maintenance costs (they only require removal or dirt and debris) and providing a cooler building for your employees.
- Lightweight: Coatings are durable but also lightweight, so they don’t add stress to your existing roof.
- Reliable: Most Coating systems can be recoated every 8-10 years to lengthen its lifespan and ensure heat reflection and waterproofing.
- Productivity: Unlike adding a new roof, applying a coating system won’t disrupt your business. With minimal noise and odor, it’s business as usual at your commercial property.
Commercial Roof Coating Products
Roof coating products can be roughly divided into solvent-based and water-based varieties. Solvent-based coatings, such as urethanes and silicones, tend to last longer but can be more expensive and require greater care in their application. Water-based coatings generally emit fewer odors (one reason hospitals and universities often prefer them, Ripps says) and cost less, but may not last as long.
One type of water-based roof coating, acrylic, accounts for a large segment of the market. Many acrylic coatings are both white and reflective, says Tom Meyer, technical liaison with Coating & Foam Solutions and secretary/treasurer of RCMA. They also tend to be lower cost than many other coating products, he adds. However, these coatings may run if it rains before they’ve dried, and typically shouldn’t be applied in colder weather.
Acrylic coatings tend to be popular in the southwestern and western states, says Steve Heinje, technical service manager with Quest Construction Products. “From the Rocky Mountains to the Cascade Mountains is a good acrylic territory.”
And because silicone coatings can resist water just hours after being applied, they tend to be popular in areas that receive more rain, including Florida and the southern half of the Midwest, Heinje adds.
Urethane coatings, which generally are solvent-based, also tend to be higher in tensile strength. As a result, the coatings are both tough and flexible and resist abrasions, due to urethane’s “molecular spring,” Heinje says.
But because they’re solvent-based, urethane coatings can emit odor during application and may be more expensive than some other options. And they may be flammable, requiring special transport and storage accommodations, Heinje adds. But urethanes also have the reputation of being durable.
Both silicone and urethane coatings tend to be more expensive than other types of coatings, Ripps adds.
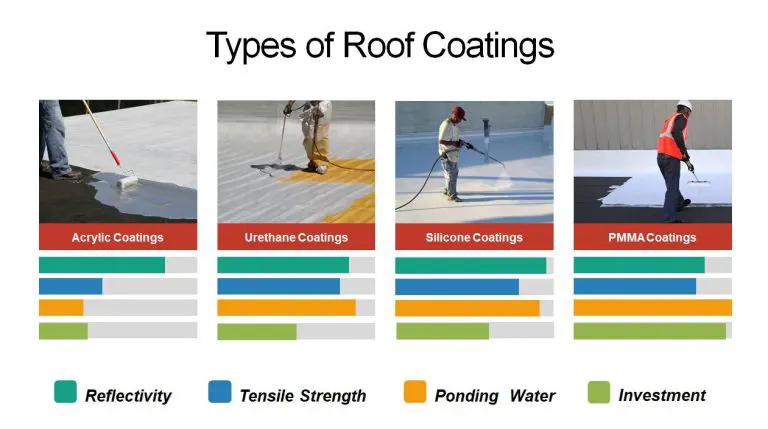
Acrylic Roof Coatings
Acrylic is a water-based, cost-effective solution for a variety of roofs. They are good for most climates and provide the best value.
Strengths: Acrylic coatings offer an excellent balance of cost and performance. They are highly reflective, UV resistant, and easy to work with.
Weaknesses: Acrylic, water-based coatings break down under ponding water over time. If it rains often and ponds remain for extended periods, these areas eventually will fail. Acrylics will lose mil thickness with weathering, need to be applied at 50°F or above, and typically do not perform well in ponding-water situations.(should add in here somewhere that they need good weather to apply because they need hours to cure before any rain)
Polyurethane Roof Coatings
Polyurethanes are more impact resistant and handle traffic the best of all coatings. There are two main types of polyurethane roof coatings: aromatic and aliphatic. Aromatic coatings are less expensive and not UV stable, so they are usually used as a base coating. Aliphatic coatings are more expensive, but are UV stable, hold color well, and stay cleaner than most other coatings.
Strengths: For durability, urethane coating systems have stood the test of time and have proven able to withstand ponding water when applied appropriately. A urethane roof coating system with an aromatic base and an aliphatic top coat is durable, stays cleaner, and is more resistant to ponding water than an acrylic coating. They also do well as cool roofs because they can be white and stay clean. (once applied, a urethane coating is not affected by rain)
Weaknesses: They are more expensive than acrylics and can have a stronger odor compared to most other coatings.
Silicone Roof Coatings
Silicones are moisture cured and humidity can even promote their cure. In some applications, the use of silicone can eliminate the need for a primer.
Strengths: On commercial low-slope roofs, the ultraviolet (UV) stability of systems silicone coating systems are unmatched. Silicones weather better than other coatings with almost no erosion and they don’t get hard or brittle. Silicone is also good in ponding water situations.
Weaknesses: Silicones hold dirt and rain act as a cleaner; therefore the material loses reflectivity over time. It is also hard to adhere to silicone, so when a roof needs re-coating, you must either remove the coating completely or re-coat with a compatible silicone. Resistance to tearing is a mechanical weakness and silicone coatings should be used with fabric as a common practice.
There are many choices when it comes to coatings, but all are cost and energy efficient and can be a good solution instead of a full roof tear-off and replacement.
What Roofs Can be Coated?
Almost all types of commercial roofs can be coated. Some examples include metal, spray polyurethane, single-ply, modified bitumen, Built-up roof (BUR) systems, etc. Without special treatments, ballasted and gravel surfaced membranes are not typically acceptable roof surfaces for coating membranes.
How Much Does a Commercial Roof Coating Cost?
The cost of a roof coating for a commercial building can vary based on many factors including repairs needed on the roofing system prior to the application of the coating and warranty type. However, the average price for a flat roof coating is $3.00 – $5.00 per square feet.
Caution about Roof Coatings
Failed or failing roof systems. A roof coating is not a substitute for roof replacement when conditions such as widespread wet insulation or loss of roof-system adhesion exist. Coatings might restore the roof’s watertight nature in these situations for a short time. But factors such as the freezing and thawing of wet insulation, membrane splitting under the coating, wind-uplift damage at un-adhered areas, and hail damage of weakened areas still can occur. In such cases, managers would be wiser to invest in a replacement roof system.
For a roof coating to work as intended, a few preparatory steps are critical. One is a thorough inspection to determine the state of the roof, says Joe Mellott, director of business development with The Garland Company. If the insulation is wet or the roof is severely damaged, it may need to be torn off and replaced; a roof coating won’t compensate for these faults. (I believe code requires a roof that has 25% or more wet damage to be replaced)
When the true condition of a roof is difficult to determine, engaging a roofing professional to examine it may make sense. The roofing professional can use such tools as thermal scans to determine if moisture has been absorbed into the roof insulation or if it has other weaknesses that aren’t readily apparent, Sosinski says. While this comes at a cost, it may end up saving tens of thousands of dollars if it becomes clear the roof doesn’t need replacing. “If the roof is dry and in good shape, you can extend its life,” he adds.
With roof coatings and restoration from Advanced Roofing, Inc., you can extend the life of your current roof at a more affordable price. For a complimentary, no-obligation estimate, call 800-638-6869 or click here to submit an online quote request.
More Info
Tags:
You may also like
Pay for It Once or Twice: The True Cost of Choosing the Wrong Roofing Contractor
In the fast-paced and weather-challenged environment of Florida, choosing the right commercial roofing contractor isn’t just a financial decision—it’s a critical business investment. Property owners and facility managers often find themselves focused on one thing:...
Roofing Price Increase in Florida: What You Need to Know in 2025
Roofing Price Increase in Florida: What You Need to Know in 2025Several economic and trade-related challenges are causing roofing material costs to rise in Florida and across the U.S. Here are the three most significant factors:The ongoing trade tensions between the...
Hurricane Damage and The Claim Process
Hurricane Damage and The Claim Process If your commercial property has experienced hurricane roof damage, planning a comprehensive recovery strategy is essential to ensure your building returns to its pre-storm condition. At Advanced Roofing, we specialize in...