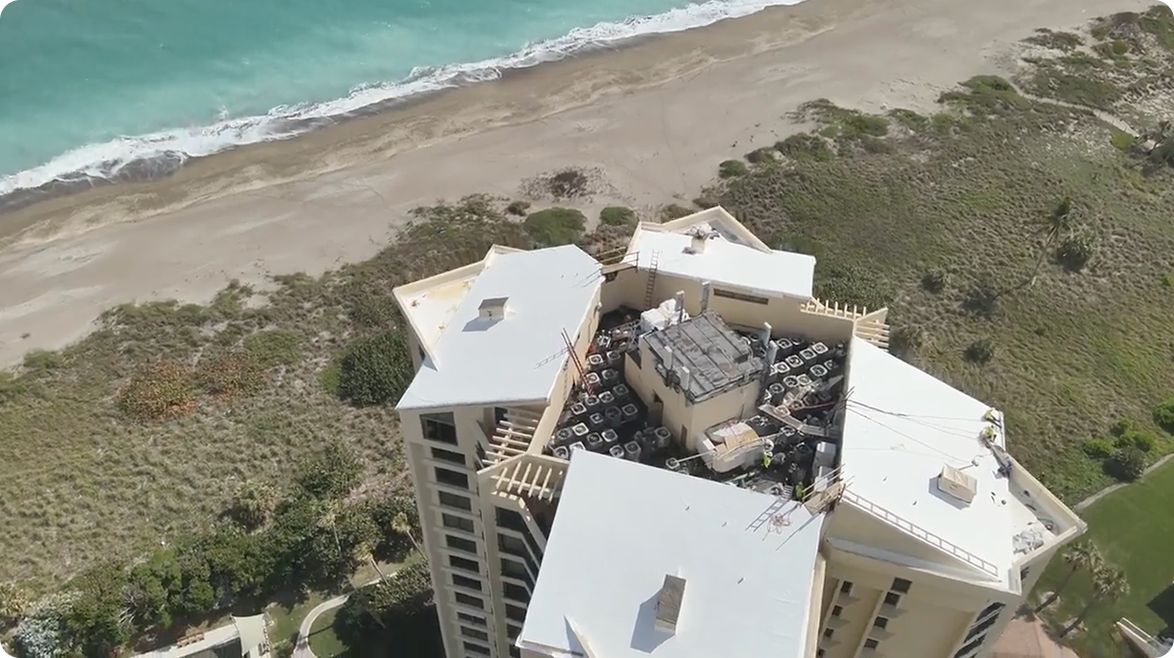
Sea Scape II Condominium
Project Background
- Main Flat Roof & Popups – Modified Bitumen (torch temp, adhered ISO & Coverboard, Torch 2).
- Perimeter Narrow Flat Roofs – Single-ply (torch temp, adhered ISO & Coverboard, adhered Single-ply KEE).
- Sloped Roofs – Adhered PVC Fleeceback over ISO & Coverboard.
Challenges & Solutions
Client Needs & Challenges
The owner’s insurance company – required the reroofing to be completed within specific deadlines for policy renewal.
The main flat deck – was highly congested with 62 AC unit condensers, restricting mobility.
The unexpected concealed roof system – on the sloped sections required re-engineering and revised permitting.
Minimizing disruptions – to residents during the AC unit work was a critical priority.
Solutions Implemented
Efficient Layout of AC Unit Lines – By reorganizing redundant AC lines, Advanced Roofing improved accessibility and streamlined the work process.
Creative Project Management & Coordination – The team worked closely with the construction manager and foreman to meticulously plan each project phase and adjust as needed.
Dual Tasking for Efficiency – Roofing crews worked on two simultaneous jobs in the same area, ensuring budget adherence and project timeline maintenance.
Special Requirements & Execution
The project had unique challenges due to safety and compliance requirements:
- Safety Protocols for Elevated Work – The combination of flat and steep-slope roofing at 170’ height necessitated advanced tie-in safety measures.
- Engineering Adjustments for Unexpected Findings – The rough finish on the concrete deck required an alternative roofing system that eliminated the vapor barrier while maintaining durability.
- Cost-Saving Modifications – By re-securing plywood over the existing standing seam metal system instead of complete removal, Advanced Roofing saved the owners significant costs while maintaining structural integrity.
- Drainage Optimization – Engineering calculations were scrutinized to avoid unnecessary scupper openings, preserving the building’s exterior and preventing additional costs.
Project Outcome
- On-Time & On-Budget Completion – Despite unexpected conditions, the project remained within the planned budget and timeline.
- Innovative Cost-Saving Strategies – Avoided excessive tear-offs and unnecessary material replacements, leading to substantial savings for the client.
- Minimal Disruption to Residents – Strategic scheduling and efficient AC unit line reorganization ensured a smooth experience for condominium occupants.
- Enhanced Safety Measures – Creative safety tie-in solutions were implemented to manage the challenges of working at extreme heights.
Why This Project Deserves Recognition
- Complexity of Mixed Roof Types at Extreme Heights – TThe project involved both flat and sloped roof systems at 170’ high, requiring specialized safety protocols.
- Swift Problem-Solving & Engineering Adaptations – Adjusting to unforeseen conditions, such as concealed roofing layers and rough concrete deck surfaces, without delays.
- Cost-Effective Innovations – Implementing revised solutions that provided financial relief to the owners without compromising quality or warranty compliance.
- Strong Team Coordination – Effective collaboration between the project manager, superintendent, foreman, and consultant ensured seamless execution.